Our services
We offer comprehensive solutions for your successful projects. From the manufacture of complex precision parts, through assembly, heat and surface treatment, to delivery anywhere in the world!
Send us your technical drawing and leave the rest to us!
An example of our production
Why us?
Engineering is a passion for us. Finding exceptional quality in each part we produce is a challenge we like to accept.
Our values

quality is our first priority.
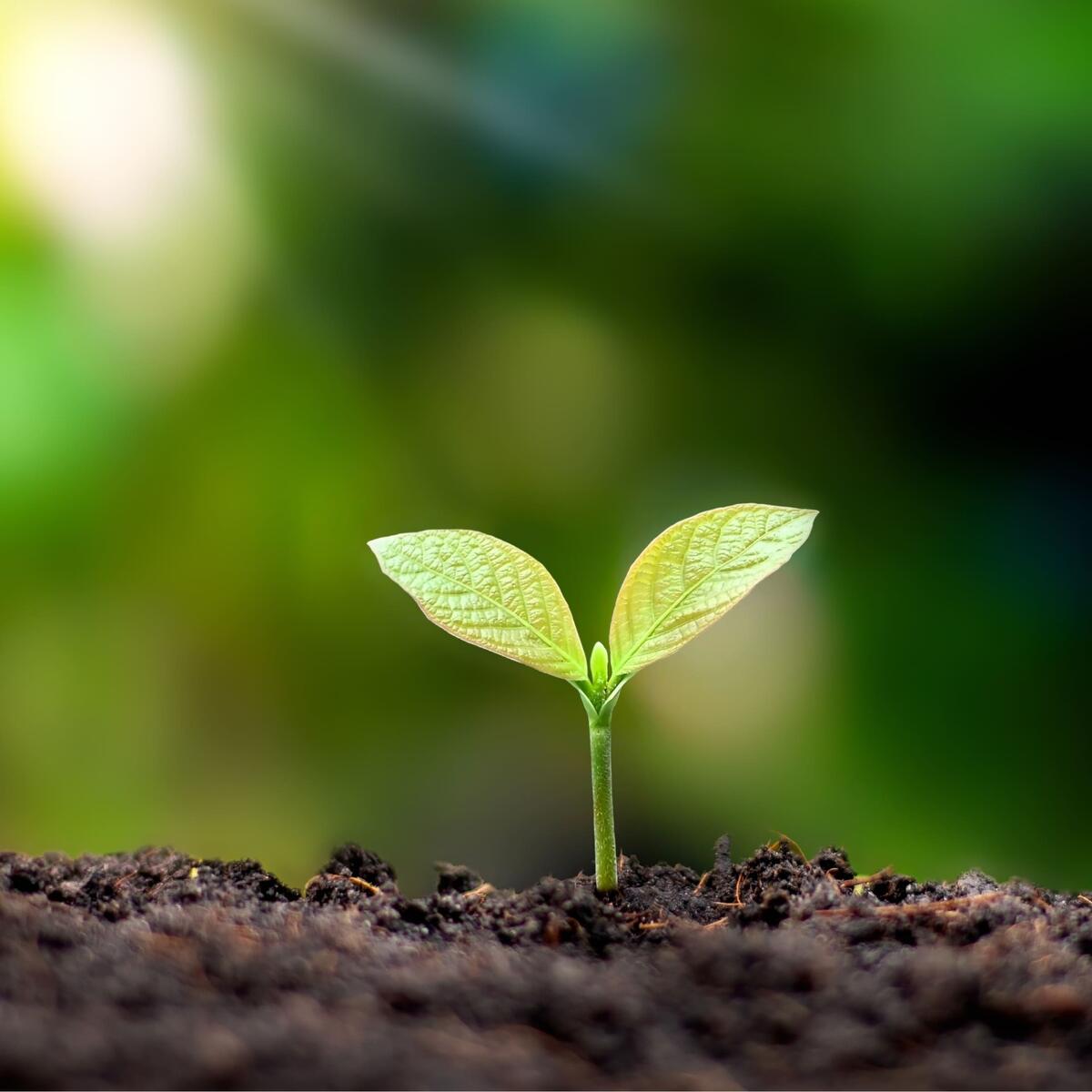
Environmental responsibility
we constantly strive to reduce the environmental footprint of our production processes.
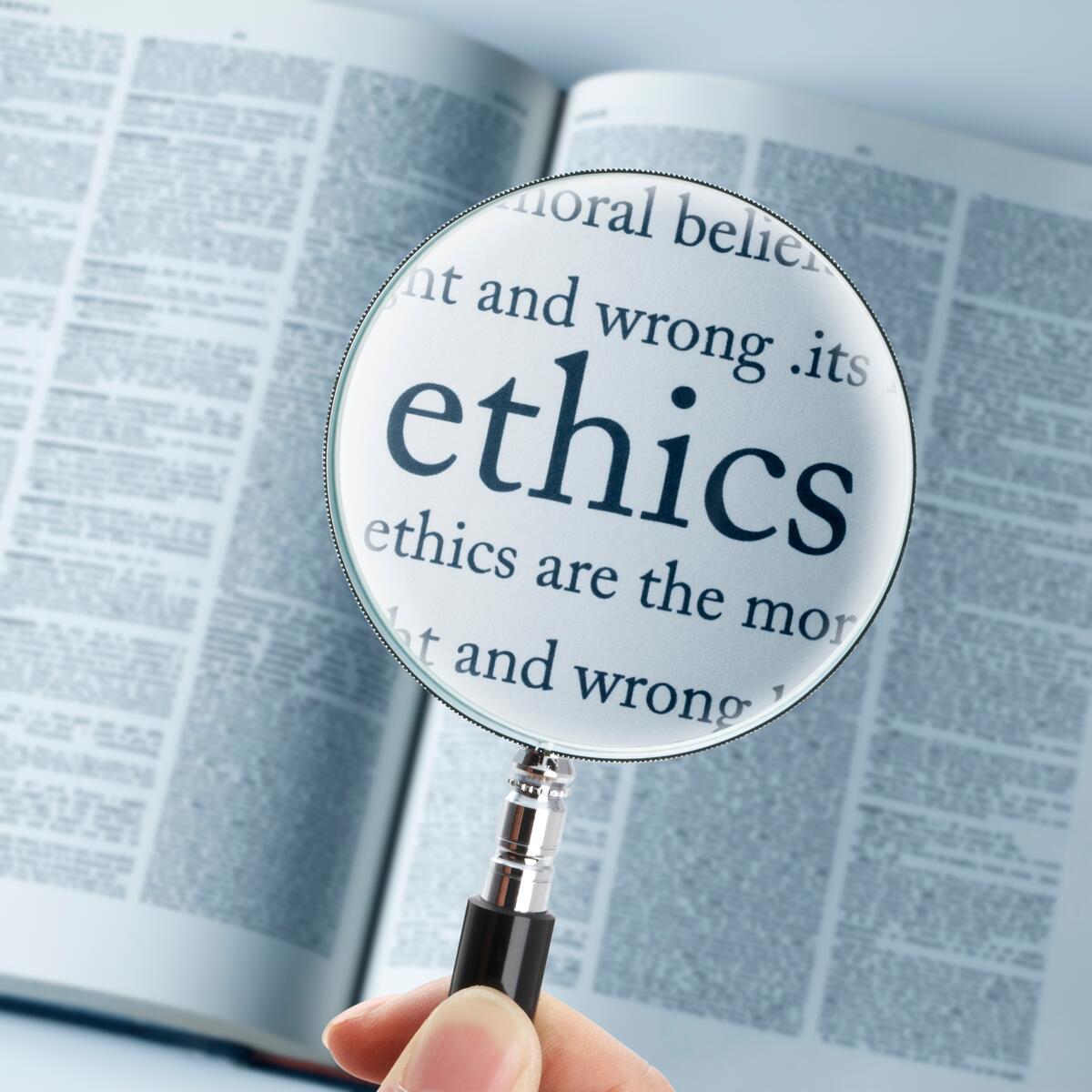
we follow a code of ethics that guarantees integrity, transparency, and fair dealing in all our activities.
Where do we deliver?
You can find our parts absolutely everywhere
They allow you to pack confectionery, medicines, or even fly across the sky.
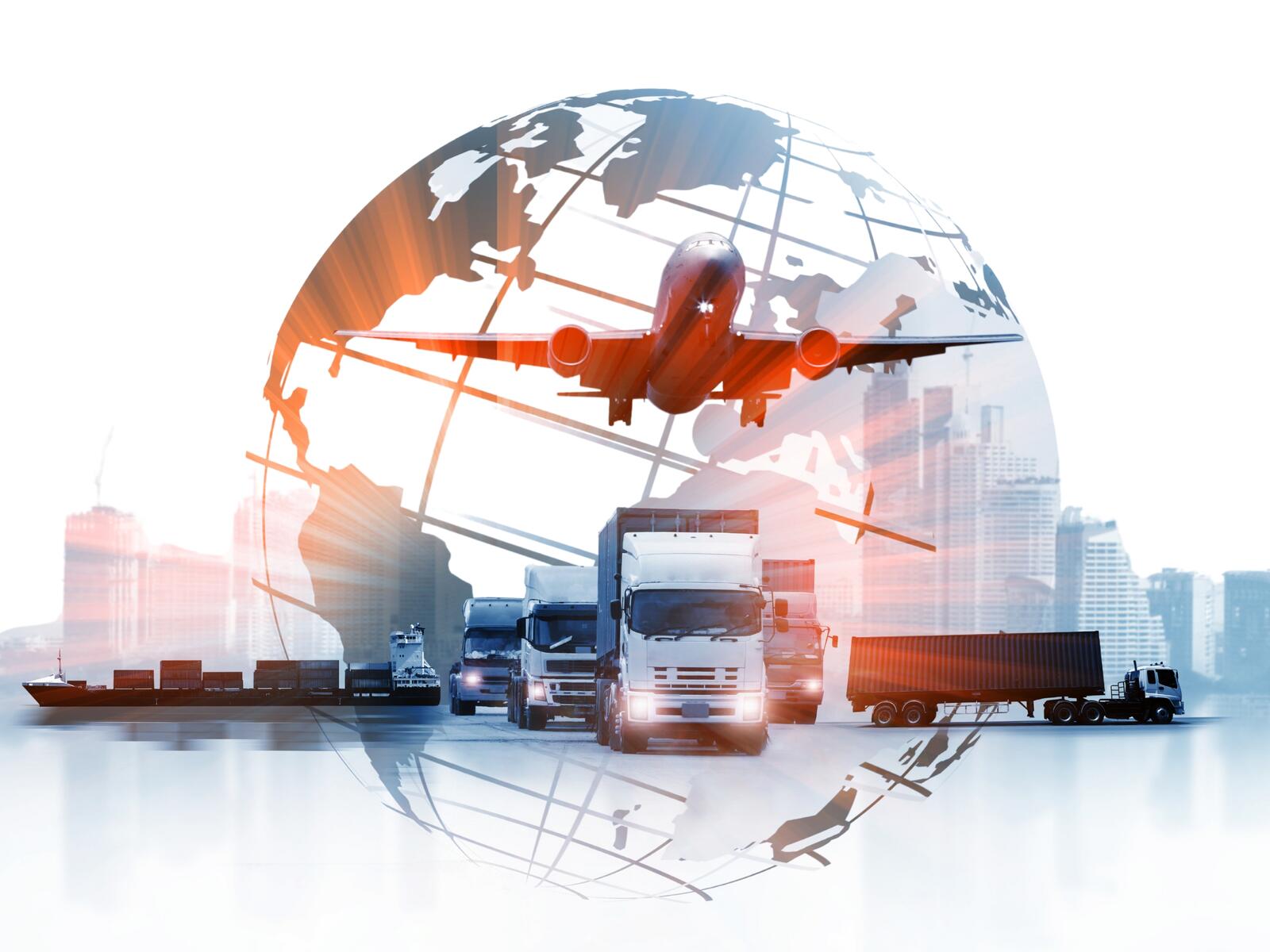
Worldwide shipping
We will transport your order wherever you need it. Quickly, securely, and at the lowest price possible.
Our prominent customers
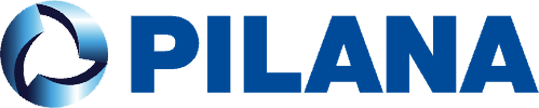
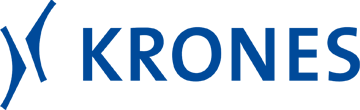




What’s next?
Cooperation
A reliable solution to ensure project success. You, too, can count on our 30 years of experience in industry!
Our cooperation takes place in the following steps.
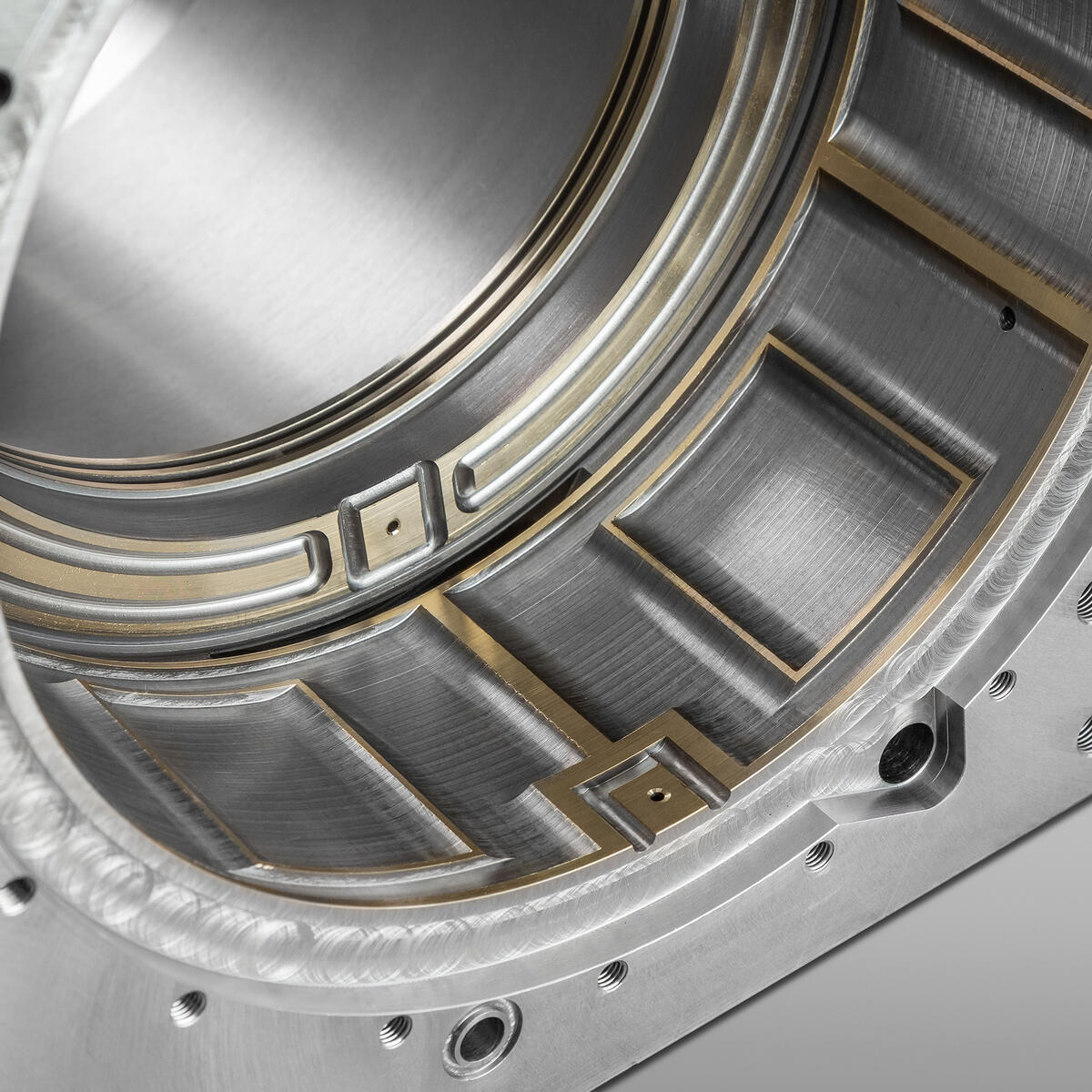
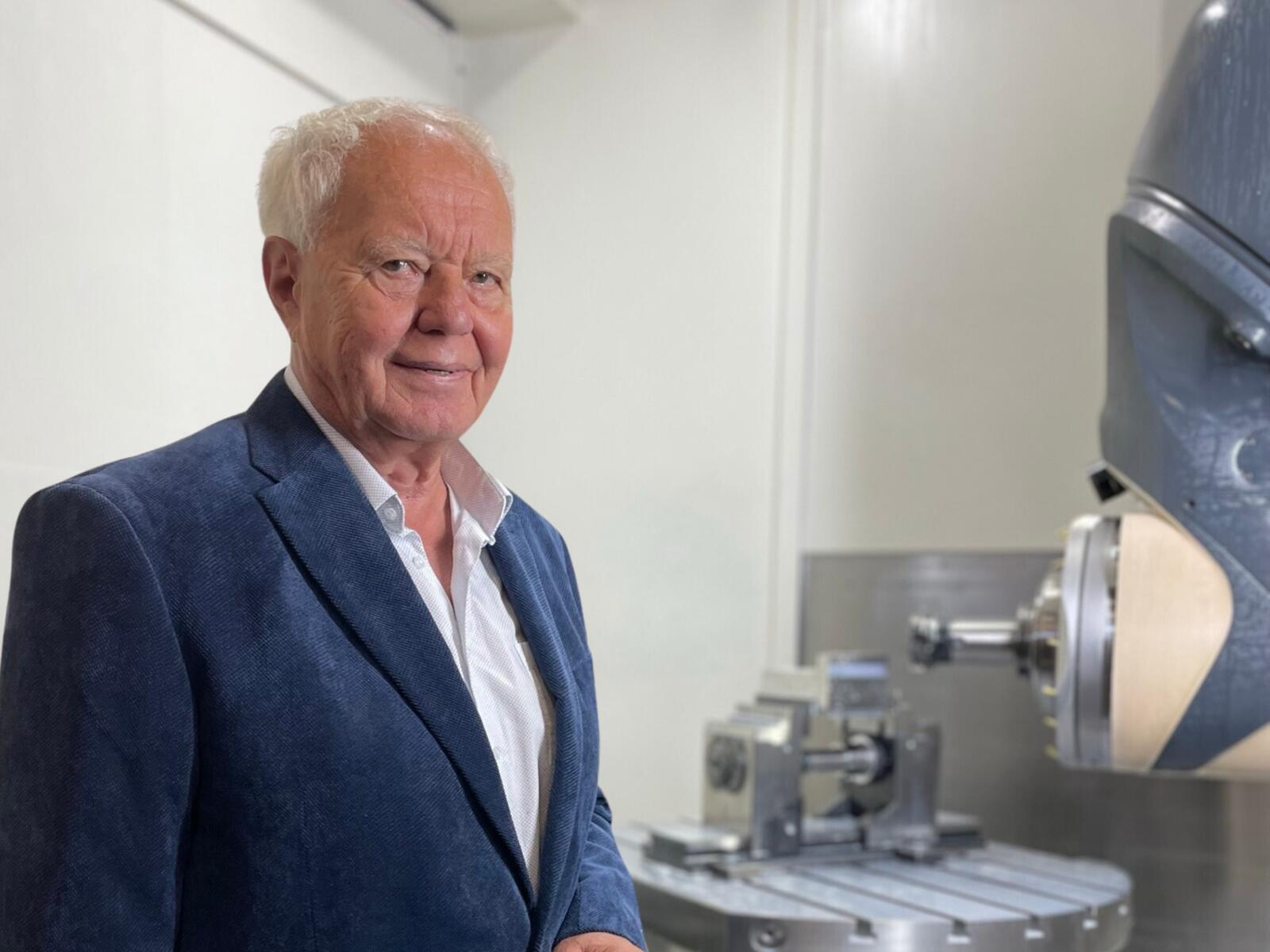
We love challenges – we have now been pushing the boundaries of precision for oursatisfied customers for 30 years.
In today’s world of extremely rapid technological progress, we are very much aware that the decisive factor is primarily people. It is all our employees who create our daily successes and contribute to our superb results.
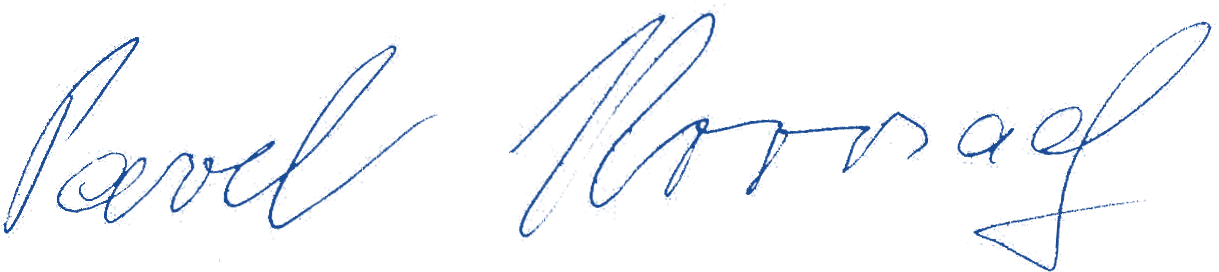
Pavel Novosad, Founder
Frequently asked questions
Are you ISO 9001 certified?
Yes, our company GENICZECH-M, spol. s r. o. is ISO 9001:2016 certified. This certificate ensures that our processes and services meet high quality standards and that we continuously work to improve them, taking into account the needs and expectations of our customers. You can therefore rely your parts being produced to the highest standards, which guarantees the quality and reliability of the products and services delivered.
What part dimensions do you produce?
We specialize in the small-batch production of machined parts. We have a wide range of modern machines that allow us to produce parts in different dimensions and tolerances. See the information on maximum part dimensions for various types of machining below:
- Lathe: We manufacture turned components with diameters ranging from 10 mm to 660 mm, which allows us to flexibly respond to diverse requirements of our customers.
3-axis milling: Our 3-axis milling machines can machine parts up to maximum dimension of 3,000 × 1,500 mm, allowing us to process large pieces of material.
5-axis milling: We also use 5-axis milling, especially for the most complex and precise parts. Using this equipment we are able to machine cylindrical parts with a diameter of up to 800 mm and a height of up to 600 mm.
Flat Grinding: Our surface grinding machines can machine parts up to 1,200 × 520 mm, allowing us to achieve high precision and excellent surface quality.
Circular Grinding: For rounded parts, we offer grinding with a maximum diameter of 250 mm, which is great for finishing turned elements.
We always strive to meet the requirements of our customers and offer optimal solutions for the production of their parts. Should you have any specific requirements or questions about your project, do not hesitate to contact us. We are here to help you find the best solution for your needs.
How long will it take to deliver my order?
Regular parts can be dispatched within 6 weeks from being ordered. If special surface/heat treatments are required, the time is extended by 1–2 weeks.
How much will it cost us?
We will tell you the price after receiving the complete production documentation, ideally with a 3D model of the part. We usually process a quote within 3–5 business days.
What measurement reports do you provide? Can you arrange for complete part metrology with possible certification?
Our company has a comprehensive measurement and quality assurance system that allows you to have full confidence in the accuracy and quality of parts produced for you. For each part that we produce, we are able to provide dimensional reports according to your specifications and requirements. We can draw up these reports based on our own standards or we can use your template.
We also provide various types of attestations, including 2.1, 2.2, 3.1, FAI, and REACH and RoHS compliance statements. If you need to perform special tests such as capillary tests or pressure tests up to 0.8 MPa, we are also ready to provide these services.
Our equipment includes a Wenzel XO 55, a cutting-edge 3D measuring machine which allows us to accurately measure both conventional and more complex spherical shapes, and to compare 3D contours with a digital model of the part. In addition, we also have other precision measuring tools such as roughness meters, altimeters, and micrometers, primarily from renowned manufacturers like Mitutoyo.
Our company is certified according to ISO 9001:2016, which ensures that all our processes and measuring reports comply with the highest quality standards.
If you have further questions about our measurement reports or need additional information, please do not hesitate to contact us. We are here to help and ensure that you are fully satisfied with the results of our work.
Can you provide me with surface or heat treatment?
Yes, at GENICZECH-M spol. s r.o. we are able to provide surface treatment and heat treatment for parts that we have produced ourselves. Surface and heat treatments are an important step in the manufacturing process, which increases the durability of the product and its aesthetic quality. So you can count on us to provide you with a complete service when we manufacture parts for you. More information about surface and heat treatments can be found here.
If you have specific requirements or need further information about the options and types of finishes we offer, please do not hesitate to contact us. We are here to provide you with a complete and high-quality service tailored to your needs.
Will you assemble my line if I deliver my own parts?
No, we at GENICZECH-M, spol. s r.o. perform assembly work exclusively for units and machines that have been manufactured by us. Because we have complete control over the entire production process from start to finish, this approach allows us to ensure the highest possible quality and reliability of the final assembled units. If you are interested in comprehensive services, including the production of parts and their subsequent assembly, we will be happy to discuss your requirements and offer you a solution tailored to your needs. Contact us for further information and cooperation opportunities.